Whether you’re looking for a new roof or want to spruce up your home, metal roofing can be an attractive option. It’s durable, low-maintenance, and energy efficient.
However, some issues that can affect a metal roof’s performance and longevity may arise. You can avoid many problems by choosing a reputable contractor, conducting regular inspections, and maintaining your roof. Contact Metal Roofing Montana now!
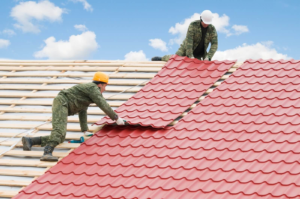
One of the main reasons homeowners choose metal roofing is because it’s a very versatile option. It comes in various color options, from neutrals like silver and gray to earth tones or bright hues such as red, blue, and green. Additionally, there are many different panel styles and finishes. You can select a smooth and sleek surface for a modern aesthetic or a textured finish that replicates the look of wood, slate, or tile for a more traditional style.
Metal roofs also offer a lot of design versatility in terms of shape and size. For example, they can be curved or angled to match the slope of your home’s structure. They can even be designed to mimic the look of traditional shingle roofs. This flexibility in design is a big advantage of choosing a metal roof because it allows you to customize the way your home looks.
Besides offering versatility in design, metal roofs are also very durable and long-lasting. They are resistant to fire, hail, and wind and can withstand hurricane-force winds. They are also highly energy-efficient and can help you save on your energy bills. Additionally, they can boost your home’s resale value and increase its curb appeal.
Another important feature of metal roofs is that they are lightweight, which makes them easier to install and remove than other types of roofing. This is especially beneficial for re-roofing projects. Furthermore, metal roofs can be installed over any existing roofing materials. Therefore, they are a good choice for those looking to upgrade their current roof without spending a fortune.
The versatility of metal roofing is also evident in the way they are manufactured. For example, a standing seam metal roof can be fabricated using steel of various thicknesses and finishes. This flexibility in production allows contractors to design a roof that will complement any architectural style.
Another advantage of choosing a metal roof is that it can be designed to accommodate attic venting. In a shingled roof, this is accomplished by running a strip of shingles along the peak of the roof. In a metal roof, however, the continuous ridge vent (CRV) can be fabricated in the same material as the rest of the roof. This can enhance the look of the roof and hide the outflow holes.
Durability
Unlike asphalt shingles, which can crack or disintegrate with extensive wear and tear, metal roofs are highly durable. Their durability also makes them resistant to fire and harsh weather conditions like high winds and heavy rains. This longevity can greatly reduce maintenance costs, making metal roofs a wise choice for property owners.
However, the durability of a metal roof is dependent on climate conditions and the type of roof. For example, strong winds can test the stability of screw-down panels or standing seams and potentially cause uplift if the roof is not properly installed. Similarly, heavy hail can damage the surface of softer metals like copper or aluminum, leading to premature corrosion. In addition, freezing temperatures can lead to moisture buildup that may damage the structure of the roof and corrode fasteners.
In these situations, protective coatings can be used to shield the roof from abrasion or other damage, while high-class insulation can keep the building cool and conserve energy. While metal roofing can withstand extreme conditions, it is important to have regular inspections to catch any signs of wear early and avoid costly repairs. Moreover, it is critical to have your roof installed by a professional with lots of experience. This is because a poor installation can make the roof susceptible to rust spots, corrosion and even leaking.
Aside from being extremely durable, metal roofing is eco-friendly and sustainable. It is made of recycled materials and can be recycled at the end of its life, which helps to reduce environmental impact. Additionally, it enhances energy efficiency by reflecting sunlight rather than absorbing it, which can lower air conditioning costs.
In terms of cost, metal roofs can be more expensive than other roofing options, such as shingle roofs. However, the longevity of a metal roof can offset this initial investment, as it will likely outlast other roofing types. In addition, metal roofs offer a variety of color options and can be customized to fit the aesthetics of the building.
Environmentally friendly
Most homeowners today are concerned about the environmental impact of their homes. Many have started purchasing eco-friendly appliances and gadgets to reduce their carbon footprint. In addition, many are looking to choose green roofing products that will help protect their home and the environment. In fact, a metal roof is one of the greenest choices a homeowner can make when it comes to re-roofing their property. A metal roof lasts longer than traditional shingles, helps to lower energy bills, and will help to protect the environment from extreme weather events.
The materials used to fabricate a metal roof are often repurposed from scrap metal, which eliminates the need to manufacture new material and reduces waste. Also, when a metal roof reaches the end of its lifecycle, it can be recycled without any loss of quality. This is in stark contrast to asphalt shingles, which cannot be recycled and will eventually end up in landfills.
Since a metal roof is often designed to reflect heat rather than absorb it, it can help cut down on a building’s energy consumption. This, in turn, cuts down on air conditioning costs and reduces a company’s or household’s monthly bills. The metal roof’s reflective properties can also minimize the impact on the climate and the surrounding ecosystems by reducing a building’s greenhouse gas emissions.
Because a metal roof has fewer cracks and creases than a shingle roof, it can be less susceptible to fire damage. This makes it a good choice for anyone living in a wildfire-prone area. Furthermore, a metal roof can significantly reduce noise pollution by mitigating external sounds. This makes for a peaceful and tranquil home environment, which can enhance well-being and diminish stress.
In terms of maintenance, a metal roof is much easier to maintain than a traditional shingle roof. Regular inspections and cleaning are typically all that is required to keep a metal roof in peak condition. This can help to save time and money for a homeowner, as well as help to reduce the burden on municipal water supplies, which is beneficial to the environment.
Maintenance
Metal roofs are known to have a long lifespan, but it’s important to perform regular maintenance to keep the material looking its best. Taking care of minor issues, such as surface scratches or dents, can help prevent water leaks and other problems that can be costly to fix. In addition, a fresh coat of paint can enhance the curb appeal of your home.
Cleaning the roof on a regular basis helps to remove dirt, leaves, branches, and other debris that can retain moisture and rust the metal materials. During this maintenance, you should also clean gutters and downspouts regularly. A buildup of leaves, sticks, and other debris can clog the gutters and cause them to fill with water, which could corrode metal roofs or attract pests to the property. Using the proper equipment, such as a ladder or an extension pole, is essential for safely and effectively cleaning your roof.
If your roof has valleys, you will want to regularly inspect them for leaves or branches that have gotten stuck. In some cases, it’s best to hire a professional to clean these areas and properly dispose of the debris to prevent scratching that could ruin your roof’s curb appeal. Additionally, it’s a good idea to trim branches that are close to your roof to prevent them from being knocked against the metal panels during storms and other weather conditions.
Lastly, it’s essential to regularly check the fasteners and sealant around vents, chimneys, skylights, and other roof penetrations to make sure they are in good condition and are securely fastened. This is crucial for ensuring that the roof has a watertight seal and protecting the interior of the building.
Maintaining a metal roof is an excellent way to preserve its durability and increase the value of your property. A well-maintained roof shows that the building is well-cared for, which can draw in potential buyers and tenants and ensure the longevity of the structure. In addition, a routine inspection can catch any issues early on and prevent them from worsening over time, which could lead to expensive repairs or even a replacement roof.